Winding machine selection
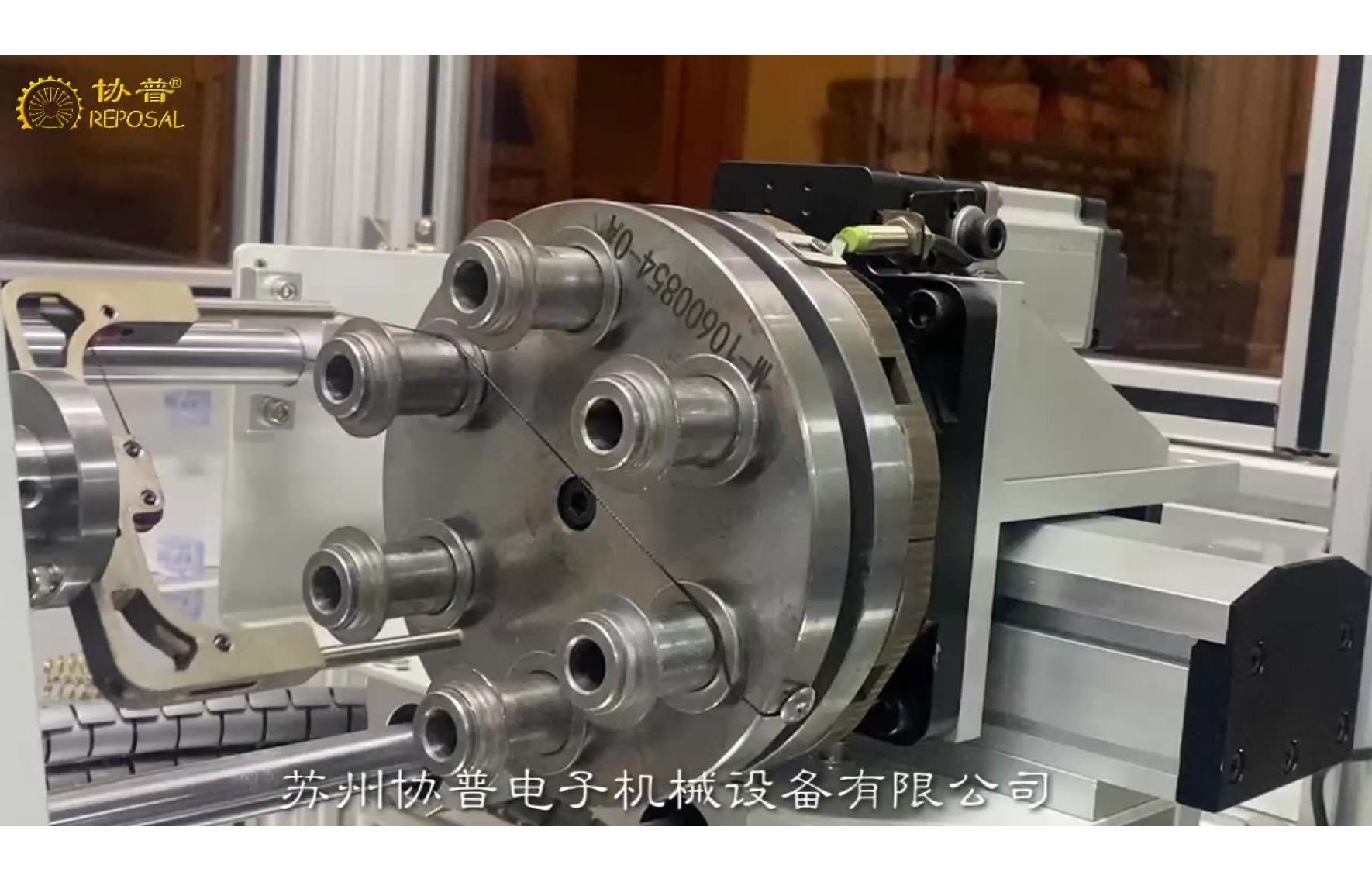
In the narrow sense, the winding machine mainly refers to the winding machine of various enamelled wire coils, these coils may be transformers, relays, inductors, current transformers, various sensors, these coils can be seen everywhere in our lives, the common feature is to use enamelled wire winding, the difference is according to the design requirements, and the cost and efficiency requirements of industrial products, Its winding process is not corresponding, so derived from a variety of different winding machine, we show on the official website is only a part of the conventional winding machine, and some are customized, or special industries are not displayed, if you need to know, you can contact us.
Coils can be seen everywhere in our lives, such as the electric meter in the home, there are metering induction coils, trip coils in the circuit breaker, transformer coils in the community, various motor coils in industrial automation, various sensor coils, starting coils on the car, ignition coils, power motor coils on the bullet train, etc., it is no exaggeration to say that we live in a world of coils. There are so many coils, and the corresponding winding machines are different, so the winding machine is as important to the electrical world as the lathe is to the mechanical world.
There are so many types of winding machines, if you are not familiar with them, those selections have become a big problem, we now make a simple introduction from several aspects.
One is the winding method, which is generally divided into parallel winding machine, toroidal winding machine, and flying fork winding machine.
Parallel winding machine: most of the cylindrical coil and rectangular coil, enameled wire and enameled wire are approximately parallel, the main structure of this winding machine is a motor control winding shaft, the other motor control axis, the two axes with interpolation relationship to move, rotate a certain Angle around the axis, the axis is moved a corresponding distance.
The parallel winding machine has two different layouts according to the direction of the shaft, one is the right side of the shaft, and the majority of the single-axis machine uses this direction, because it is conducive to right-handed operation during the winding process, and more importantly, the operator can easily observe the arrangement of the winding, which is especially important for high-demand coils. There is also a positive out of the shaft, it is because of the need for high frequency loading and unloading of the coil skeleton, the advantage of the positive out of the shaft is that the skeleton is pulled in the direction of the operator's chest, and the skeleton is pushed forward by the operator, so it is more labor-saving, but its disadvantage is that due to the concentration effect of the eyes, it is difficult to observe the winding quality of the coil in real time.
The high frequency loading and unloading of the front shaft is mainly determined by the number of turns of the coil, such as the process speed of a winding machine is 3000RPM, which can be wound 50 turns per second, if the number of turns of a coil is only 100 turns, then two seconds after the start can be wound to complete, such as the speaker voice coil is a typical coil, the machine dynamic rate of this coil is relatively low. The loading and unloading cycle accounts for the entire point-to-point cycle is relatively large, so the loading and unloading frequency is very high, but its number of turns is small, by controlling the process rigidity and control accuracy of the winding machine can ensure the winding yield, so this product will be used in the entire industry.
The same is the front winding machine, if my coil turns reach 3000 turns, the same is the winding speed of 3000RPM, then the front winding machine with two axes will be used, one minute after the start of the winding two coils, and then the skilled operator can complete the loading and unloading of two products in about 10 seconds, in one minute of winding time, Can operate the disassembly of another winding machine, which is also front two axes, and carry out other finishing work. This is based on the actual efficiency to make the choice, similarly, if my coil number is 5000 turns, I will choose a four-axis front exit winding machine.
The above is a brief introduction of parallel winding machine, in addition, tension control, process rigidity, control accuracy, clamping method, etc.
The second is the ring winding machine, the ring winding machine refers to the coil skeleton is a closed ring, we want to be in the closed ring is radial wound enameled wire, the typical product is the transformer, used to sense the current through the center of the ring coil, its main feature is that the enameled wire diameter is small, but the number of turns is more, this application is very long, in the initial process route, It is manually completed by people, the enameled wire is first wound on a cylindrical I-wheel, and then the operator manually holds the I-wheel inside and outside the ring.
Later, people improved the process, the I-wheel is installed on a rotating ring, the ring will have an opening, and then the ring skeleton is placed in the open ring, the open ring with the I-wheel rotation, the enameled wire is automatically wound to the ring skeleton.
Then, with the cost pressure, people need to design a smaller ring coil, the open ring with the I-wheel through the ring skeleton requires a larger space in the middle of the ring, obviously can not meet the requirements, people will design the open ring as an open closed ring, and then open a storage slot along the outer cylinder, the paint coil first wound to this storage slot. This open ring with a wire storage slot has a new name - wire storage ring. When the wire storage ring rotates, the enameled wire in the wire storage slot is released to the ring skeleton in different ways. This design minimizes the size of the ring skeleton and the specifications of the enameled wire, greatly reduces the material consumption, and provides greater freedom of design.
There are three ways to release the enameled wire of this ring winding machine. One is to use a shuttle-shaped member of the wire belt, which is matched with the dovetail groove on the release side of the storage ring, so that the wire belt can slide around the storage ring during the winding process. This way is suitable for relatively thin enameled wire, because in the process of releasing the enameled wire through the wire belt device, The enameled wire has a back bend in one direction on the wire carrier, and the curvature of this back bend is large, and the thicker enameled wire is not suitable. The ring winding machine is defined as a side-slide winding machine, which means that the take-up wire device slides on the side of the storage wire ring.
Then for the relatively thick enameled wire how to release, people have a corresponding scheme, in the storage ring round surface in the concave shape of a synchronous belt, so that the lacquer bag in the release side pressure between the storage ring and the synchronous belt, in this way of winding process, the return curvature of the enameled wire edge slide is much smaller, in addition, This method is not suitable for thinner enameled wire because of the large pressure between the synchronization belt and the storage ring, and the thinner enameled wire is very easy to break due to pressure and friction between the storage ring and the synchronization belt. We call this type of ring winding machine called belt type ring winding machine, it also has an obvious disadvantage, the enameled wire is released in the pressure of the synchronization belt and the storage ring, if the pressure is too large, even if we treat the storage ring very smooth, or may appear to scratch the insulation layer of the enameled wire, but the pressure is too small, it can not make the enameled wire winding tight collapse, which is on the inductance, consistency, Cost all makes a difference, especially thicker enamelled wire. It was clear that we needed a winding solution with thicker enamelled wire.
In addition to the original storage ring, a gear drive ring is separated. In the storage stage, the drive ring drives the storage ring, and in the release stage, the drive ring drives a wire strap to drag out the enameled tape in the storage ring. A friction mechanism is recorded inside the storage ring when dragging. This mechanism adjusts the winding tension of enameled wire, and this structure solves the winding problem of thicker enameled wire, but it has several disadvantages, one is because the driving ring is a gear structure, whether it is an open type big gear or a detachable big gear, it will cause its speed not to be high, and the second is that the release is actually driven by the wire strap to drag the enameled wire storage ring. Therefore, the enamelled wire requires a certain tensile strength, which determines that it cannot be applied to thinner enamelled wire.
The above is the introduction of the gear type ring winding machine and its three structures.
Flying fork winding machine:
The biggest difference between the flying fork winding machine and the parallel winding machine is that the parallel winding machine is the winding skeleton in rotation, and the enameled wire is continuously released in the skeleton, while the flying fork winding machine is the skeleton does not rotate, and the enameled wire is wrapped around the skeleton, which is mainly suitable for the occasions where the skeleton is not suitable for rotation, such as the external winding motor rotor coil, U-shaped transformer coil, C-shaped transformer coil, etc. Winding of longer flexible frames.
According to the different wiring methods, it is divided into parallel flying fork winding machine and rotating flying fork winding machine, parallel flying fork winding machine is the diameter of the wire swinging, applied to U-shaped mutual inductance coil, or a long flexible skeleton winding, and the rotating flying fork winding machine is the skeleton swinging.
The above is a brief introduction to the conventional winding machine, specific to the selection of time, but also combined with the requirements of the product, such as the same ring coil, the transformer ring coil is characterized by the small diameter of the enameled wire but the number of turns, and the common mode inductor requires both sides of the coil alignment consistent inductance consistent. For example, the same parallel winding coil, the requirements in the civilian relay coil is very low, the coil can be roughly flat in the skeleton bone, but the same parallel winding coil, the fiber guidance coil needs to be in the tens of kilometers of fiber winding process, all the requirements of constant tension row, so the requirements of the two are actually very far apart.