Research and development background and characteristics of precision current transformer winding machine
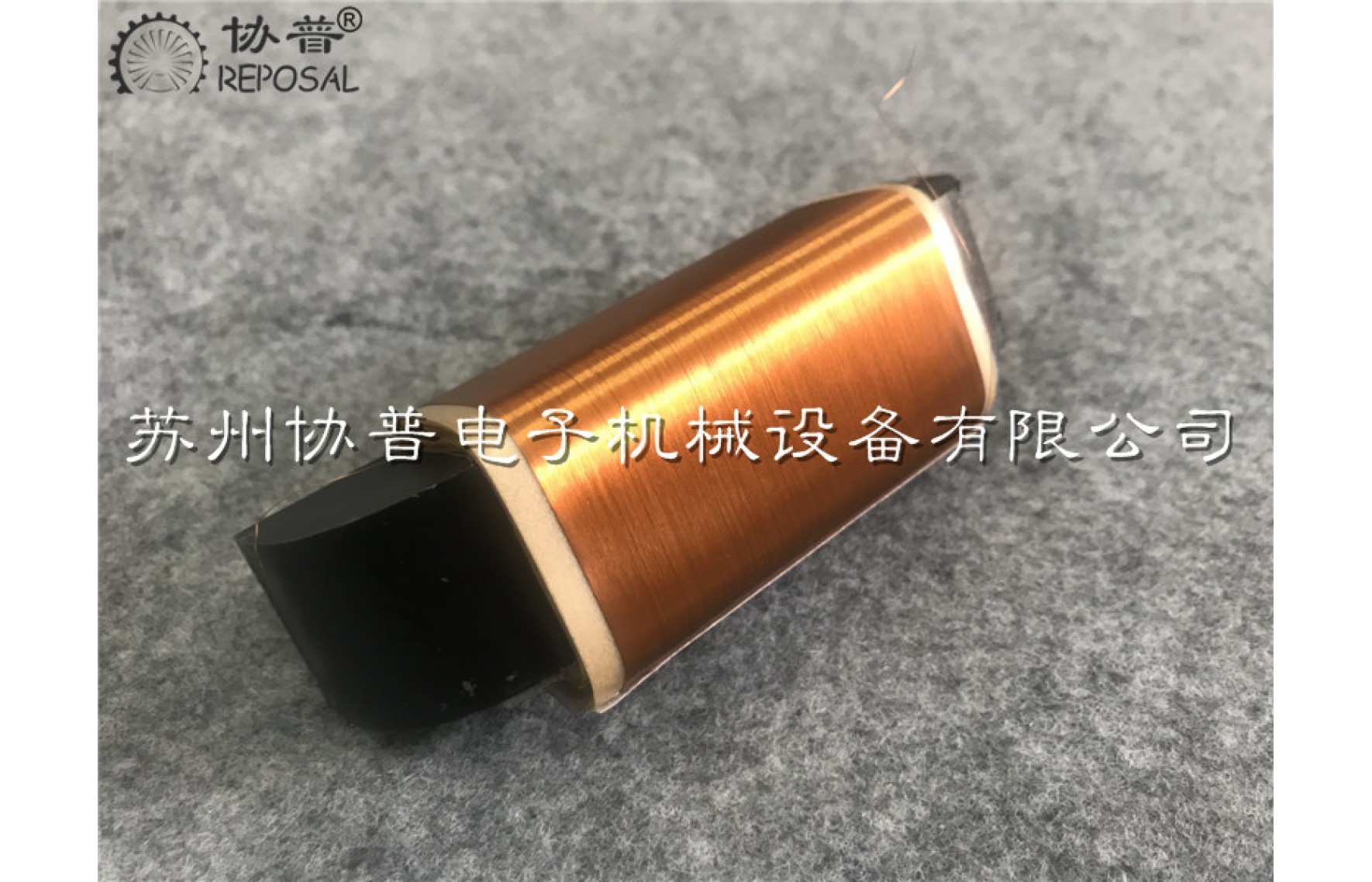
Research and development background and characteristics of precision current transformer winding machine
The precision of coil in current transformer is very important, because it directly affects the accuracy of current measurement and the reliable operation of power system. The specific importance of coil accuracy is reflected in the following aspects.
Electrical energy metering: In a power system, accurate measurement of current is the key to calculating energy consumption. If the coil in the current transformer is not accurate, it will lead to an error in the measurement of electrical energy, which can lead to a miscalculation of energy costs, with possible financial implications for both the utility and the consumer.
Fault detection: The current transformer is used to monitor the current level to detect abnormal conditions in the power system, such as short circuit and overload. If the accuracy of the coil is not high, it may lead to false positives or neglect of potential faults, which affects the reliability of the power system.
Overcurrent protection: Current transformers play a key role in overcurrent protection devices, detecting overcurrent events and triggering circuit breakers or other protective devices. The accuracy of the coil directly affects whether the overcurrent can be accurately detected to ensure the safety of the power system.
Load management: The load management of a power system requires accurate measurement of current in order to make reasonable load distribution and adjustment. If the precision of the coil is not high, it may lead to unbalanced load distribution, affecting the efficiency and stability of the power system.
Automated control: In modern power systems, automated control systems rely on accurate current measurement data for real-time adjustment and control. The precision of the coil is critical to the response speed and performance of the system.
Waveform analysis: Current transformers are also used for power quality analysis, including harmonic analysis. The precision of the coil determines the accurate analysis of the current waveform, which helps to solve the power quality problem.
In short, coil accuracy is critical to the performance and application of current transformers. High-precision coils ensure the accuracy of current measurements, thereby maintaining the reliability, stability and efficiency of the power system. Therefore, when selecting and using the current transformer, it is very important to ensure that the accuracy of the coil meets the application requirements.
Through the above introduction, we already know the transformer coil for the transformer described an impact and its importance, then the following content, let's introduce, how to obtain high-precision transformer coil, to this end, we have developed a high-precision transformer coil winding machine. The picture shown in this article is the coil of a type c current transformer.
As can be seen from the picture of this product, the core of a C-type current transformer is cut by a rectangular rectangular core. The customer then requested that the coil be wound directly around the long side of this cut core. The enamelled wire of this product is 0.2 mm in diameter and 2700 turns. Because it is a mass production, it requires high precision, does not allow for chaotic lines, a lot of layers are wound, and requires stable production.
We carefully listen to and collect the needs of customers, targeted to develop the transformer winding machine they need, and successfully meet the needs of customers. On this basis, the transformer winding machine is summarized.
High precision current transformer coil winding machine is a kind of equipment specially used for manufacturing current transformer coil, it plays a crucial role in the manufacturing process of current transformer. People in the actual high-precision transformer production, for the current transformer coil winding machine.
Automatic production: High-precision current transformer coil winding machine using automation technology, can automatically complete the coil winding process. This automated production method increases production efficiency, reduces labor costs, and reduces the possibility of human error.
Accuracy and consistency: The high accuracy of the transformer winding machine ensures that each current transformer coil has consistent characteristics. Specific performance in the number of turns accurate, orderly, tension stability of these three aspects. This is essential for the accuracy of current measurements, especially in applications where high precision is required.
High-speed winding: High-precision current transformer coil winding machine usually has high-speed winding function, can complete a large number of coil manufacturing in a short time. This is very important for mass production of current transformers.
Adjustment flexibility: The winding machine usually has adjustable parameters, such as the number of turns of the coil, the wire diameter and the winding speed. This allows the production process to be flexibly adjusted to different models and specifications of current transformers.
Customization ability: Because different current transformers may have different specifications and requirements, the corresponding fixture and even the equipment structure are different, high-precision current transformer coil winding machine usually has a certain customization ability to meet the needs of different customers.
In short, the high-precision current transformer coil winding machine plays an important role in the current transformer manufacturing, they ensure the performance and accuracy of the current transformer through the automatic, high-speed and accurate coil winding process. These machines have a wide range of applications in power systems, including power metering, power protection, power quality analysis and other fields.
Now let's briefly introduce the current transformer itself.
Current transformer An instrument that converts a large current into a small one. Like magic, it has an iron core and a bunch of coils. One pile of coils is wound around the line to measure the current, while another pile of coils is strung around the measuring instrument and the protection device. The secondary side of the CT is always closed, so it acts like a super short circuit.
Okay, now let's talk about what's going on. On the power supply line, the size of a current ranges from a few amps to tens of thousands of amPs. But we usually need a stable secondary current to measure, protect and control the power system, because the primary voltage is usually high and direct measurement is very dangerous. This is where the current transformer comes in.
The current transformer has two windings: the primary side (few turns) is strung in the current line to be measured, and the secondary side (more turns) is strung in the measuring instrument and protection loop. The ratio of the primary side current (I1) to the secondary side current (I2) of the current transformer is called the actual current ratio K. For pointer ammeters, the secondary current of the current transformer is usually in the ampere-scale, while for digital meters, their sampled signal is usually in the milliampere-scale.
The model of the current transformer is usually indicated by letters and numbers, such as L for current transformer. The letters in the model number can indicate its type, installation, insulation, and so on.
As for the technical parameters, rated capacity, primary rated current, secondary rated current, rated current ratio, etc., are very important indicators. There are many types of current transformers, such as measurement and protection, and their working principles and requirements are not the same.
Finally, it should be noted that electronic current transformers are gradually emerging, and they have the advantages of diamagnetic saturation, low power consumption, wide band, etc., so in the power system, current transformers are a very critical component. Hopefully this colloquial explanation will help you better understand the principle and application of current transformers.
Let's talk about how to choose the current transformer!
First of all, the rated voltage is higher than the rated voltage of the line, which is very important.
Next, the variable ratio. The ratio of the current transformer should be calculated according to the primary load. There are generally a variety of specifications to choose from, such as 20, 30, 40, 50, 75, 100, 150 and 2 x a/C. Where 2×a/C indicates that the same product has two current ratios, which can be switched by changing the wiring mode of the connection piece. In general, if the load current in the line is 350A, then you should choose a ratio of 400/5. If it is used for protection, a larger variable ratio can be selected to ensure accuracy.
Next is the choice of the level of accuracy, which is determined according to the accuracy requirements of the measurement. The accuracy level of the current transformer used for billing and metering is not less than 0.5, and the ammeter used to monitor the current of the incoming and outgoing line circuit should choose a current transformer of 1.0 to 3.0.
The second is the verification of dynamic stability and thermal stability, which can be verified according to the following formula:
Dynamic stability check: Kes×I1N ≥ ISh
Thermal stability check: (KtI1n)²t ≥ I∞tima
Then there is the rated capacity, the secondary rated capacity of the current transformer is greater than the actual secondary load, usually 25% to 100% of the secondary rated capacity. This can affect the accuracy of the measurement or control, so be aware.
Finally, some considerations for use:
The wiring should comply with the series principle, the primary side is connected in series with the circuit under test, and the secondary side is connected in series with all instrument loads.
Choose the appropriate ratio according to the size of the measured current, otherwise the error will increase.
The secondary side must be grounded to prevent the high voltage of the primary side from entering the secondary side when the insulation is damaged, resulting in a safety accident.
Never open the secondary side, otherwise there will be high voltage danger, and do not disassemble ammeter or relay equipment without bypass during operation.
In short, when the current transformer is working normally, the secondary side is used in series with current coils such as measuring instruments and relays, so it should be operated carefully to ensure safety.