Compared with mechanical gyroscopes, fiber optic gyroscopes have no moving parts, impact resistance, high sensitivity, and long life. Therefore, fiber optic gyroscopes are widely used in high-precision and high-speed positioning scenarios and will gradually replace electromechanical gyroscopes.
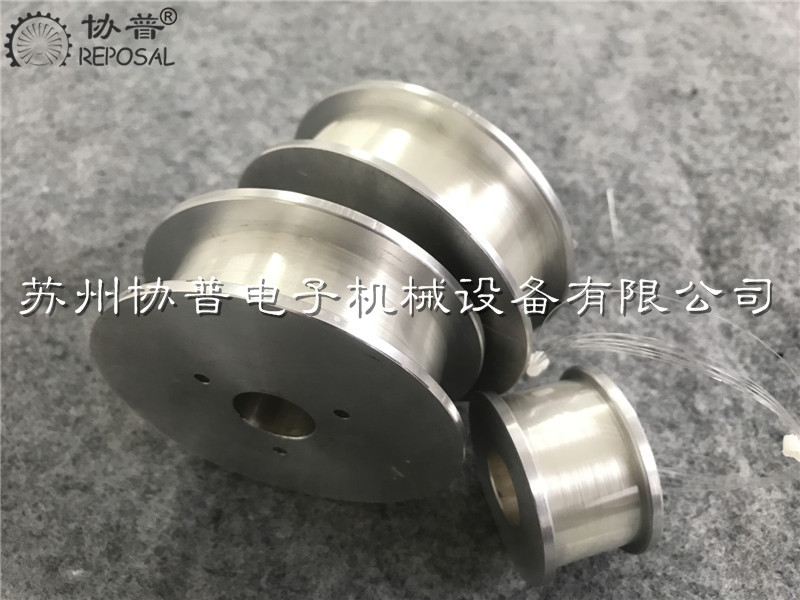
The basic components of the fiber optic gyroscope are the optical path and the circuit, and the fiber is the core component of the gyroscope. The fiber winding machine for preparing high-precision fiber coils has also become the key point of the gyroscope.
However, due to the blockade of its related technologies, the fiber optic gyro winding machine has always been a key technology insurmountable. REPOSAL® Electronic Machinery Co., Ltd. actively develops fiber optic gyro winding machines in response to market demand.
Through continuous research and improvement, we automate the winding process of the fiber optic gyroscope, and compare and analyze the winding methods of various fiber coils. We have obtained that the tension control and the accuracy of the winding during the fiber winding process affect the structure of the wound fiber coil. The key factor.
By optimizing the aforementioned tension control factors and winding accuracy algorithm, the effective and stable control of reasonable tension, the effective and reliable high-precision winding control, the memory of all process parameters, and the convenience of control, a new generation of optical fiber winding machine was developed and put into production .
With the practical application of research and development results, we will continue to improve and produce high-reliability and high-efficiency fiber optic gyro winding machines.