Debugging method and video of winding machine
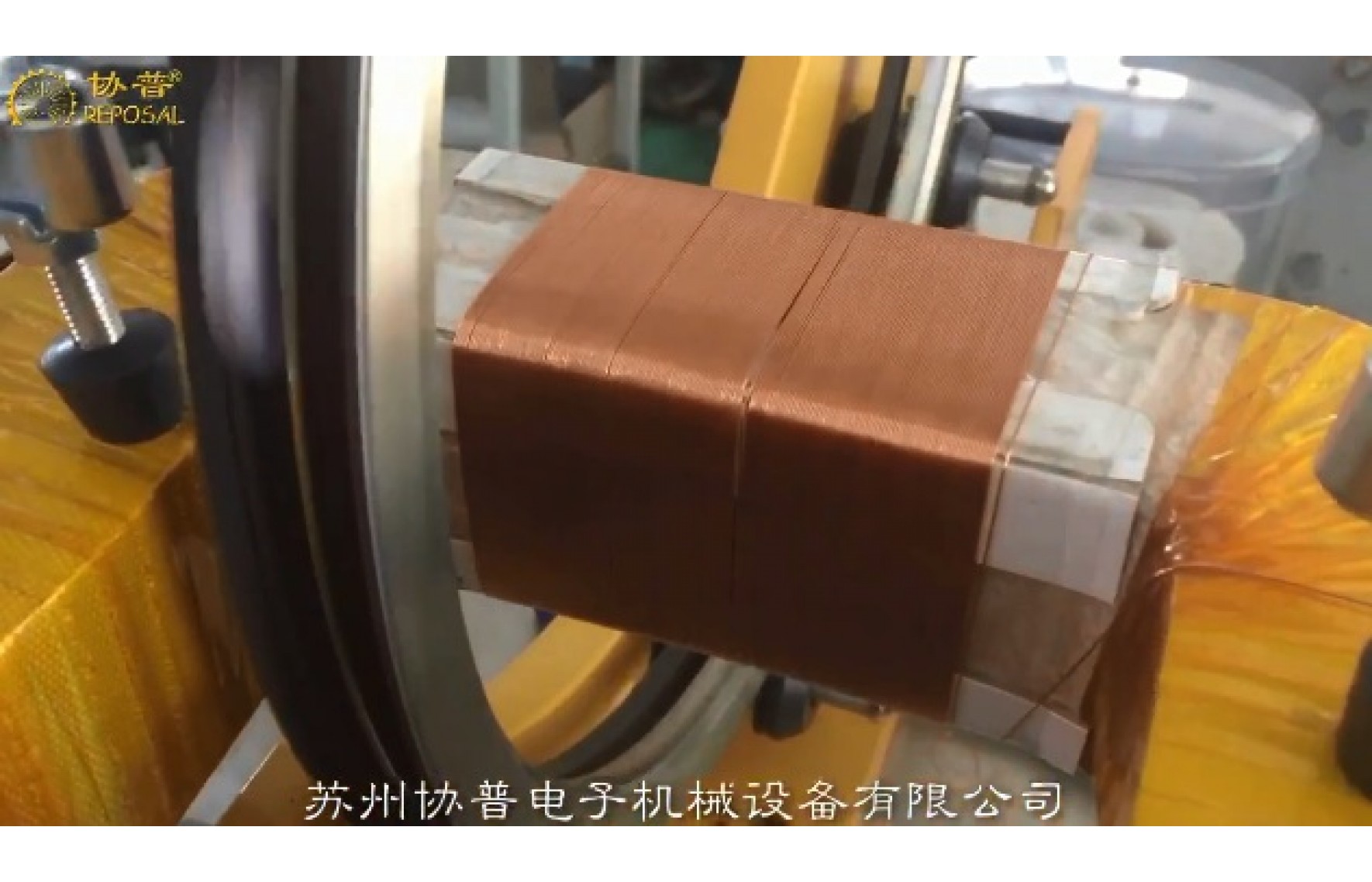
Debugging method and video of winding machine
1. Preparations before starting the winding machine.
As a kind of precision equipment, in order to keep the winding machine with good working accuracy for a long time, at the same time, the winding machine is a equipment with rotation as the main movement feature. In order to ensure the safety of the process, we need to carefully check the winding machine before the machine. Whether there is debris on the workbench, whether the screws on the winding machine are loose, whether the power switch is properly connected, whether the specification of the enameled wire meets the requirements, confirm that there are no problems with the above problems before starting the machine.
2. Parameter setting of precision winding machine
Press the reset button on the winding machine controller, or press the reset button on the front of the winding machine, the winding machine will automatically reset, at this time, if you need to set the winding machine parameters according to the production schedule. Then press the "step sequence setting" "input" button on the controller of the winding machine in turn, and then press the input key, the cursor will jump backwards in turn at the prompt light on the screen, "starting point", "width" ", "wire diameter", "number of laps", "start winding slow withdrawal", "stop slow", "high speed", "low speed", "wire direction", "winding direction" and other parameters, and finally press "confirm" "Button to confirm, and press the "reset" button to save the data and reset automatically, the parameter setting is completed.
After entering the setting interface according to the step-by-step setting input, pay attention, press the input again to scroll back, and press the-number to scroll forward. When you turn to each parameter, you can enter the corresponding number according to the actual process requirements. For this parameter, you can modify the parameter by typing in the number, or you can adjust the position in real time through the right or right key at the bottom right of the winding machine controller. At the same time, the number in the parameter box will change accordingly in real time.
When the parameters are input, press Enter, and reset will make the entered parameters take effect.
Also note that after entering the parameter setting interface, the parameters are divided into two categories, one is the digital parameter, and the adjustment method is the above. The second is the switch parameter, such as the winding direction, the winding direction, and the function of parking at both ends. Press the corresponding button once, and the indication on the button will turn on or off accordingly, which means that the parameter has been modified accordingly.
3, dry run inspection
After the winding machine parameter setting is completed, the winding cannot be performed immediately. The winding must be confirmed that the setting of the winding machine fully meets the requirements before winding. Run it with an empty car first, and pay attention to check whether the winding machine's wiring, winding turns, reset method, parking position, etc. meet the requirements. If it does not meet the requirements, you must repeat the above steps and re-adjust until the requirements are met.
4, go online
Place the enameled wire reel that meets the requirements on the bracket steadily, cover the plastic sleeve and the tube cover, and pass the wire out of the porcelain nozzle on the tube cover, pass through the wire nozzle, felt, wire wheel, and movable wire rack in turn, and finally from the activity The copper wheel of the wire frame leads out.
5, winding
Thread the wire frame with the terminal on the special positioning die of the winding machine, wind the enameled wire around the bottom wire terminal, check whether the enameled wire has a wire wheel, if everything is normal, press the red "start" button to start winding. If there is an abnormal situation in the middle, immediately press the "stop" button on the winding machine, stop and check, after troubleshooting, press the "start" button to continue winding.
Precautions:
1. The operator must pay attention to safety. After the machine is started, the hand should not be close to the rotating part. When the machine needs to be adjusted, it must be stopped first, and then adjusted. After the adjustment is completed, it must be confirmed that the hand has left the dangerous area before restarting.
2. The operator should not wear gloves while working, and the sleeves should not be too long. If the female operator has long hair, tie it up or put it in a safety helmet.
3. After winding the wire, check whether the bottom thread and the upper thread are connected to the corresponding terminals; whether there is enough looseness at the connection between the bottom thread and the upper thread and the terminal; whether the upper thread is close to the wire frame to exit; whether the coil winding appears Taper; if there are any bumps or indentations on the surface, after confirming that it is qualified, put the coil in the turnover box, and make sure that the power terminal must not touch the surface of the coil when placing it. After filling a box, make a mark on the box to prevent confusion.
4. When the coil appears to be tapered or the machine makes an abnormal sound, the operator should immediately stop the machine and find the equipment maintenance personnel for inspection and repair, and cannot make claims without authorization, so as to avoid waste of materials and damage to the machine.